Kissinger Associates, Inc.
2213 Quarry Drive, Suite 105
West Lawn, PA 19609
Featured Software
Subscribe for Business & Tech Insights
Thank you for subscribing! We have received your information and will begin sending you our business and technology insights via email.
Oops, something went wrong! Please reload the page and try again.
Strategic Partnerships and Certifications
.png)
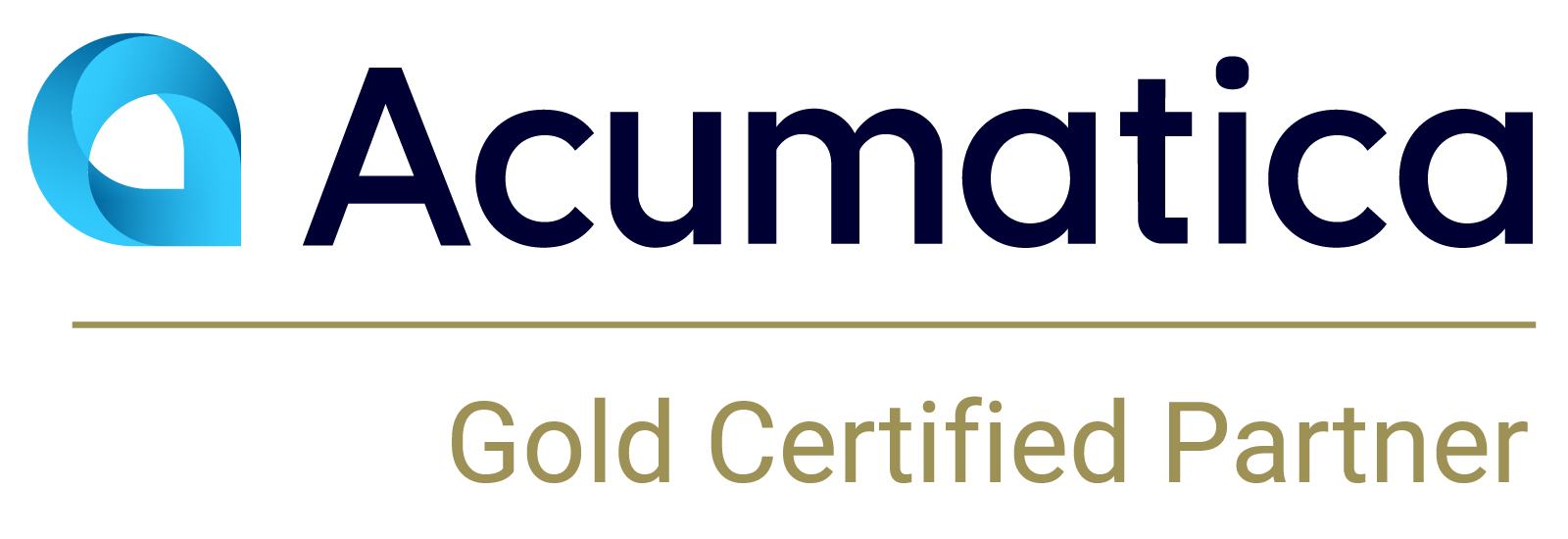

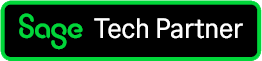
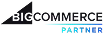